Aluminium extrusion is a fascinating process that allows for the creation of complex and sturdy shapes with ease.
Aluminium extrusion is a highly versatile manufacturing process used to create various shapes and profiles from aluminium metal. This process involves pushing or pulling heated aluminium billets through a die to form the desired shape. It is widely used in industries such as construction, automotive, aerospace, and consumer goods due to its many benefits.
Aluminium Extrusion - The Process
Step 1: Design and Preparation
The first step in the aluminium extrusion process is design and preparation. This is a crucial stage, as it sets the foundation for the entire process and can greatly impact the final product.
Designing an effective extrusion profile involves careful consideration of factors such as shape, size, tolerances, and material selection. This step requires collaboration between engineers, designers, and customers to ensure that all requirements are met for the desired product.
Once the design is finalised, preparation work begins. The first task is to select the appropriate alloy for the extrusion project. Aluminium alloys are chosen based on their properties, such as strength, corrosion resistance, conductivity, and formability.
The next step is to create a die or tooling that will be used to shape the aluminium into its final profile. Die design also plays a vital role in determining the success of an extrusion project. It must consider factors such as material flow rate, pressure distribution, and cooling techniques to produce precise results.
After designing and creating the necessary tools or dies, it's time to prepare the billet—a solid block of aluminium that will be fed into the extruder machine. Billets come in various shapes and sizes, depending on their intended use. They can range from simple cylindrical shapes to more complex profiles with multiple voids.
Before starting the extrusion process itself, it's important to clean both the billet and the die thoroughly. Any impurities or contaminants present can cause defects in the final product or damage to equipment.
Once everything is ready for production, it's essential to establish proper heating parameters for optimal results. Heating methods may vary depending on factors like billet size and the type of aluminium alloy used.
Step 2: Heating the Aluminium Billet
Once the aluminium billet has been selected and prepared, it is time to move on to the next step in the extrusion process: heating. This crucial step involves heating the billet to a specific temperature that allows it to be easily shaped and formed.
The purpose of heating the billet is twofold. First, it softens the metal, making it more malleable and easier to manipulate during extrusion. Second, it helps to eliminate any internal stresses or strains within the metal that could potentially cause defects in the final product.
The most common method of heating aluminium billets for extrusion is through a furnace. The furnace can either be gas-fired or electrically powered and is designed specifically for this stage of the process. The temperature inside these furnaces can reach up to 900 degrees Celsius (1650 degrees Fahrenheit), ensuring that the aluminium reaches its optimal temperature for extrusion.
Before being loaded into the furnace, each billet is weighed and marked with an identification number. This number allows for precise tracking throughout each stage of production and ensures quality control measures are met.
Once inside the furnace, an automated conveyor system moves each billet through different heating zones at a controlled rate. These zones gradually increase in temperature until reaching their designated set point, which is determined by factors such as alloy type and desired end-product specifications.
It is essential that every part of each billet reaches a uniform temperature before moving on to extrusion; otherwise, this could lead to inconsistency in shape or strength within the final product.
After spending several hours inside the furnace, each heated billet moves onto a cooling table, where water jets help temper and cool down its surface while still maintaining its core temperature. This rapid cooling process also helps prevent warping or distortion of the metal due to thermal shock.
Step 3: The Extrusion Process
The extrusion process involves pushing a heated aluminium billet through a die to create a desired shape or profile. This is done using an extrusion press, which exerts immense pressure on the billet to force it through the die. The temperature of the billet and the speed of the press are carefully controlled to ensure optimal results.
- Heating: The first step in aluminium extrusion is heating. The billets are preheated in a furnace to soften them and make them more malleable for shaping. This also helps remove any impurities that may be present in the metal.
- Loading: Once heated, the billets are loaded onto an automated handling system that transports them to the extrusion press. Here, they are aligned with precision and fed into the press one by one.
- Extruding: As mentioned earlier, an enormous amount of pressure is applied to the billet as it enters and passes through a specially designed steel die in an extrusion press. This transforms its cross-sectional shape into that of the die opening.
- Cooling: After emerging from the die, hot profiles go through water-cooling chambers called quench tanks, where they cool down rapidly to retain their new shape.
- Cutting: Once cooled completely, long profiles are cut according to specific lengths using saws or other cutting machines.
- Ageing: Profiles undergo artificial ageing after cutting if needed for increased strength or hardness, depending on their final use.
- Surface treatment: Profiles undergo surface treatments such as polishing or painting according to their end-use requirements before being packaged and shipped.
The extrusion process may seem straightforward, but it requires precision and expertise to achieve consistent and high-quality results. The temperature, pressure, speed, and handling of the billets are all critical factors that can affect the final product's strength, shape, and surface finish.
Step 4: Cooling and Finishing
After the extruded aluminium profile has been stretched to its desired shape, it is then cooled and finished before it can be used for various applications. This step is crucial, as it ensures the final product has the desired mechanical properties and surface finish.
Cooling:
The first part of this step involves cooling down the hot aluminium profile. The profile is moved through a series of water baths or air jets, depending on the specific cooling method used. As the profile passes through these baths or jets, it gradually cools down to room temperature. This controlled cooling process helps prevent any warping or distortion in the final product.
Stretch straightening:
Once the extruded profile has been cooled down, it may undergo stretch straightening if required. Stretch straightening is a process where rollers apply tension to stretch out any minor distortions that may have occurred during cooling. This ensures that the profile remains perfectly straight and true to its intended dimensions.
Ageing:
Some aluminium alloys require an ageing treatment after extrusion to achieve their full-strength potential. Ageing involves heating up the extruded profile at a specific temperature for a specified amount of time before allowing it to cool naturally. This process allows for precipitation hardening, which increases the strength of the alloy.
Cutting:
After the cooling and finishing processes are complete, the long piece of extruded aluminium will need to be cut into smaller sections according to specific customer requirements. This cutting can be done using saws, shears, or other methods, depending on factors such as size, shape, and tolerance requirements.
Surface finishing:
The final step in this stage is surface finishing, which improves both the aesthetics and functionality of extruded profiles. There are several options available for surface finishing, including anodizing, powder coating, painting, or polishing.
Anodising involves creating a protective layer on top of the aluminium by immersing it in an electrolytic solution and passing an electric current through it. This process not only enhances the appearance of the profile but also increases its resistance to corrosion.
Powder coating is another popular surface finishing method where dry powder paint is electrostatically applied to the profile and then cured in an oven. This creates a durable, smooth, and colourful finish that is resistant to scratching, chipping, and fading.
Painting is a similar process to powder coating but uses liquid paint instead. It can be done manually or using automated systems, depending on the volume of production.
Polishing involves buffing the extruded profile with abrasive materials until it achieves a shiny, reflective surface. This method is often used for decorative purposes and requires skilled labour as well as special equipment.
Types of Aluminium Extrusion Profiles
> Standard Aluminium Profiles
Standard profiles are pre-designed shapes that are commonly used in aluminium extrusion. These profiles are typically used for a variety of purposes, from architectural and industrial applications to consumer products. They come in a wide range of sizes and shapes, making them versatile and easy to use.
Some common types of standard profiles include T-shapes, L-shapes, U-channels, round tubes, square tubes, and rectangular tubes. These shapes have numerous applications across various industries.
For example:
T-shapes are often used as structural support beams in construction or as frames for shelving units.
L-shapes are commonly utilised in door frames or window frames.
U-channels can be found in transportation equipment such as truck beds or bus interiors.
Round tubes are popularly seen in household items like curtain rods or furniture pieces.
Square and rectangular tubes are frequently used for building structures such as handrails or fences.
Standard profiles are an essential part of the aluminium extrusion process. They offer a wide range of shapes and sizes that cater to various industries and applications. Their versatility, strength-to-weight ratio, corrosion resistance, and sustainability make them an ideal choice for many projects.
> Custom Aluminium Profiles
Custom profiles are a key aspect of the aluminium extrusion process. They allow for the creation of unique, tailored shapes and designs that are specific to a customer's needs.
The first step in creating a custom profile is designing the shape or cross-section that is desired. This can be done using computer-aided design (CAD) software or by working with an experienced extrusion engineer. The design must take into consideration factors such as the strength, weight, and functionality of the final product.
Once the design is finalised, it is transferred onto a die, which is essentially a steel block with a hollow cavity in the shape of the desired profile. The die serves as a mould for the molten aluminium during extrusion. It is made from high-strength steel to withstand the high temperatures and pressures involved in the extrusion process.
The versatility of the extrusion process allows for a wide range of custom profiles to be created, from simple shapes like squares and circles to more complex designs with intricate details. This makes aluminium extrusion a popular choice among industries that require unique and specialised components for their products.
Major Players in the Aluminium Extrusion Industry
The aluminium extrusion industry is a vast and competitive market, with numerous players vying for a share of the pie.
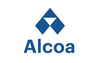
Founded in 1888, Alcoa Corporation is one of the oldest and largest aluminium producers in the world. With operations spanning across six continents, Alcoa has established itself as a global leader in both primary and fabricated aluminium products. The company's extensive research and development efforts have resulted in several innovations in the aluminium extrusion process, making it one of the major players in this industry.
Headquartered in Paris, France, Constellium is another significant player in the aluminium extrusion market. The company specialises in developing customised solutions for various industries, such as aerospace, automotive, packaging, and more. With over 25 production facilities spread across Europe, North America, and the Asia-Pacific region, Constellium has made a significant impact on the global aluminium extrusion market.
Part of the Aditya Birla Group, Hindalco Industries Limited is India's leading producer of aluminium and copper products. The company has an annual capacity of over 1 million metric tonnes of aluminium production and operates through its subsidiary Novelis Inc., which is one of the world's largest recyclers of beverage cans. With its strong focus on sustainability practices and innovative technologies like high-strength alloys for lightweight vehicles, Hindalco has become a prominent player in the global aluminium extrusion industry.
Hydro is one of the world's largest integrated aluminium companies, with operations spanning across 40 countries. The company produces primary aluminium, rolled products, and extruded solutions for various industries like automotive, building and construction, packaging, and more. With its strong focus on sustainability and innovation, this Norwegian company has become a formidable competitor in the global aluminium extrusion market.
In addition to these major players, there are also many other regional and local companies that contribute significantly to the aluminium extrusion industry. Each of these companies brings unique strengths and capabilities to the table, making it a highly competitive market with constant advancements in technology and product offerings.
It is worth noting that, with increasing demand for sustainable materials globally, the aluminium extrusion industry is expected to experience significant growth in the coming years. And with such strong contenders constantly pushing the boundaries of innovation, this sector will continue to evolve at an unprecedented pace, making it an exciting space to watch out for.